Unknown Facts About Hon Hai Precisions
Wiki Article
Getting My Mfg To Work
Table of ContentsSee This Report about MfgAll About MfgA Biased View of Additive ManufacturingOem Can Be Fun For EveryoneOem Things To Know Before You BuyMore About Lean Production
The message on this web page is an example from our complete White Paper 'Shot Moulding for Buyers' - * Sample text * - for full guide click the download switch over! Intro This overview is intended for people who are seeking to source plastic mouldings. It offers a much required understanding right into all that is involved with developing plastic parts, from the mould device needed to the moulding process itself.If you want to explore even more, the guide covers kinds of mould devices, in addition to unique completing procedures such as colours & plating. Words that are underscored can be found in the reference in the appendix ... Component I: Moulding: The Basics The Benefits of Injection Moulding Plastic injection moulding is a really specific procedure that supplies numerous advantages over various other plastic handling methods.
Precision is excellent for extremely elaborate components. You can hold this moulding in the hand of your hand and it has managers, ribs, metal inserts, side cores and openings, made with a gliding closed off feature in the mould device.
Some Known Factual Statements About Hon Hai Precision
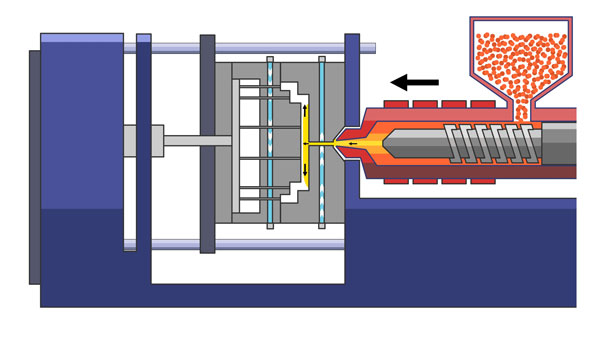

The 20-Second Trick For Manufacturing Industries
from material feed Product melting; material injection; cooling time and ejection as well as the re-closing of the mould tool ready device all set next cycleFollowing Draft angles - The wall surfaces of a moulded part must be slightly tapered in the direction in which the part is ejected from the mould device, to enable the part to be expelled quickly.Ejector stroke - The pressing out of ejector pins to expel the moulded component from the mould device. Ejector stroke speed, length as well as timing requires to be carefully managed to avoid damage to the ejectors and mould tool, but at the exact same time make the moulding cycle as brief as feasible.
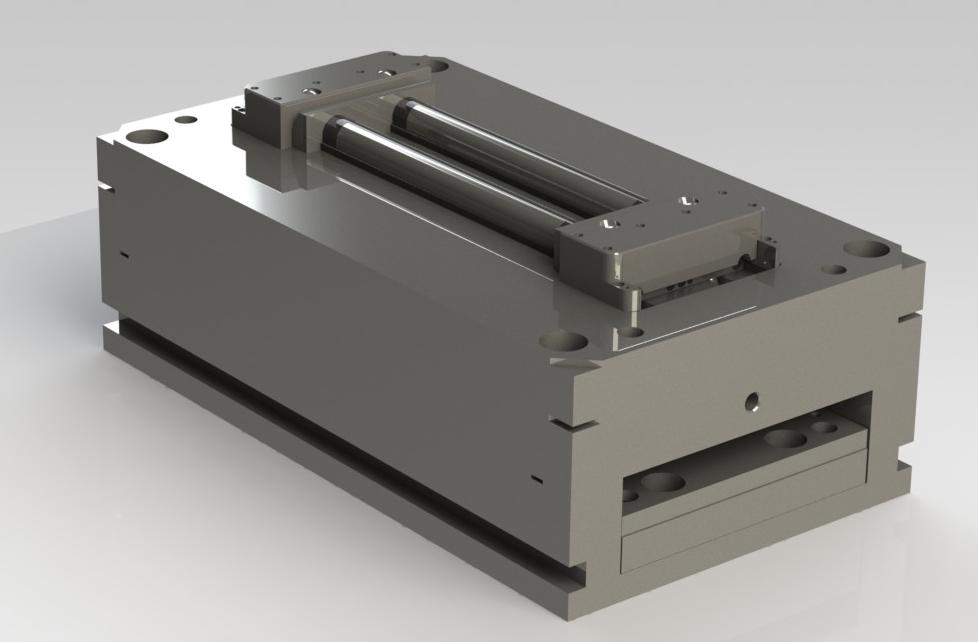
About Die Casting
Ribs - When a plastic component has thin wall surfaces, ribs are included in the layout to make the thin wall surfaces more powerful Side cores - Side activity which produces a feature on a moulded part, at an opposing angle to the typical opening instructions of the mould look at this website device. die casting. The side core needs to be able to retract as the plastic part can not be expelled otherwise.
Wall surfaces - The sides of a moulded part The text on this web page is an example from our complete White Paper 'Injection Moulding for Customers'.
Manufacturing process for generating parts by infusing molten material into a mould, or mold Simplified diagram of the process Shot moulding (united state punctuation: shot molding) is a manufacturing procedure for generating components by injecting molten material right into a mould, or mold and mildew. Shot moulding can be performed with a host of materials mainly consisting of steels (for which the procedure is called die-casting), glasses, elastomers, confections, and also the majority of frequently polycarbonate and also thermosetting polymers. Injection moulding is commonly made use of for producing a range of components, from the smallest elements to whole body panels of automobiles. Injection moulding utilizes a special-purpose equipment that has three parts: the shot unit, the mould and also the clamp.
The 7-Second Trick For Lean Manufacturing
Process qualities [edit] Shot moulding utilizes a ram or screw-type plunger to compel liquified plastic or rubber material right into a mould cavity; this strengthens into a shape that has adapted the shape of the mould. It is most frequently made use of to refine both thermoplastic and also thermosetting polymers, with the quantity use the former being considerably higher.: 13 Thermoplastics prevail as a result of features that make them highly ideal for shot moulding, such as simplicity of recycling, adaptability for a variety of applications,: 89 and ability to soften and stream on heating.In multiple dental caries moulds, each cavity can be similar as well as develop the same components or can be distinct and form multiple different geometries throughout a solitary cycle.
The screw supplies the raw product onward, blends and also homogenises the thermal and also thick distributions cnc manufacturing of the polymer, and minimizes the required home heating time by mechanically shearing the product and also adding a considerable quantity of frictional heating to the polymer. The material feeds forward via a check shutoff and accumulates at the front of the screw right into a quantity recognized as a shot. When enough material has collected, the material is required at high stress and speed into the part developing dental caries. The specific amount of shrinking is a function of the material being made use of, and also can be relatively predictable. To avoid spikes in stress, the process typically uses a transfer position representing a 9598% complete cavity where the screw shifts from a constant rate to a consistent stress control.
Manufacturing Industries Things To Know Before You Get This
The packaging pressure is applied till the gateway (cavity entrance) strengthens. Due to its small size, the gate is normally the very first site here area to strengthen through its whole thickness.: 16 Once the entrance strengthens, no even more material can enter the tooth cavity; appropriately, the screw reciprocates and acquires product for the following cycle while the product within the mould cools down so that it can be expelled as well as be dimensionally secure.Report this wiki page